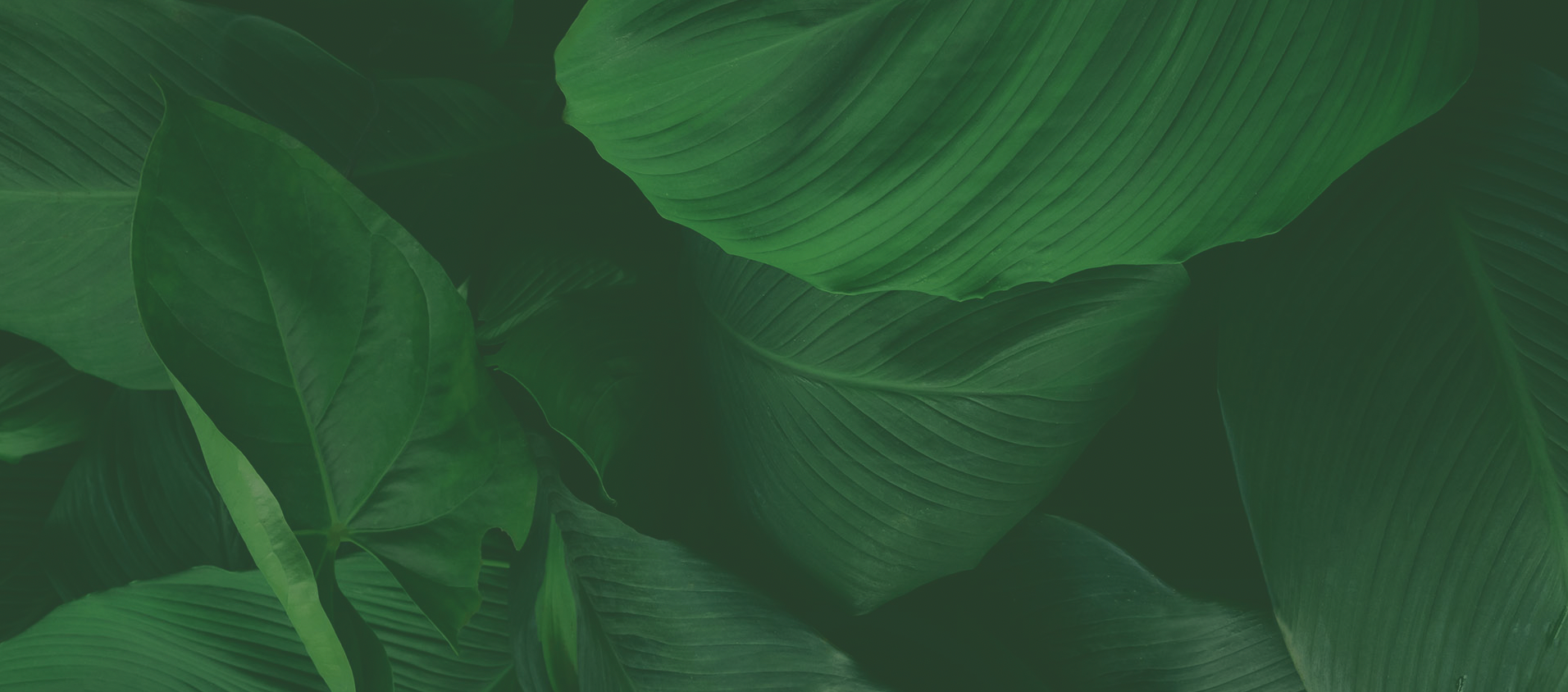
Our Commitment
Our customers set ambitious environmental goals, and AFCO’s commitment is to do everything we can to help you achieve them. That’s why sustainability efforts are a central focus for AFCO. We provide sanitation solutions that drive sustainable food safety. Together we can reduce environmental impact, working smarter and more efficiently for the sake of the future.

Trusted Partner Delivering Sustainable Solutions Through Food Safety®
Our Vision
For more than 150 years, the industry has looked to AFCO for leadership—a legacy we take seriously. Our vision is to remain a trusted partner, creating a safer food industry by delivering sustainable solutions. We do this by providing you with products and services that maximize your operational efficiencies, reducing carbon emissions, water, and waste through responsible chemistry and water management.
Our Purpose
& Values
“In partnership with our customers, we are committed to make the world a better place through food safety, and utility and labor conservation.”
PURPOSE
We are committed to food safety
PROMISE
To solve problems with responsible solutions
PARTNERSHIP
Grow and succeed together
SERVICE
Implement a plan
CONTINUOUS IMPROVEMENT
Commitment to performance and conservation
DELIVER
Quantifiable results
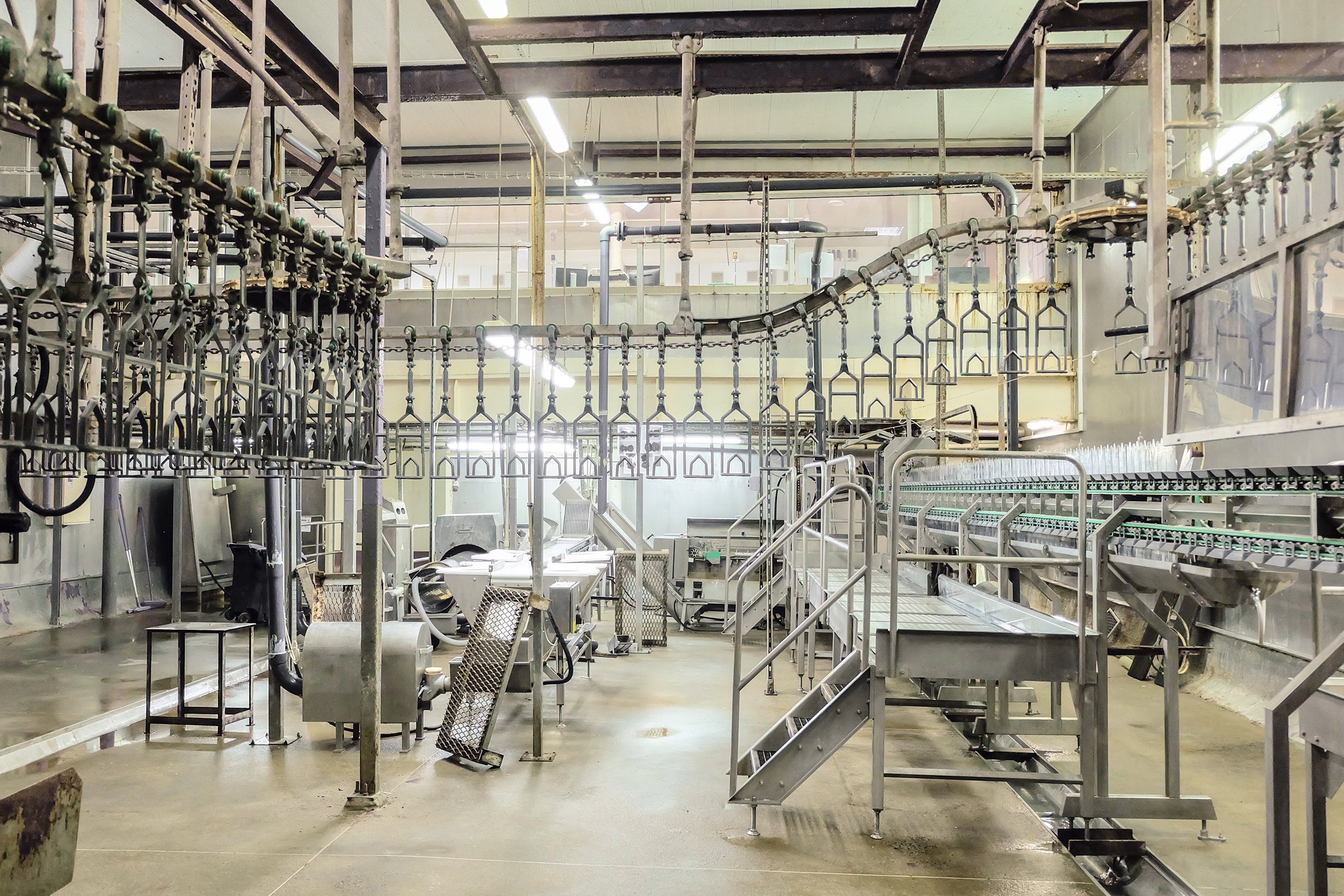
ESG Mission
OUR IMPACT
Creating A Sustainable, Safe, and Equitable Future … Together
Not many industries have the impact that we do. Together we can make a healthier planet, stronger communities, and successful businesses. All it takes is environmental stewardship, social accountability, and good governance practices. If your mission is to make a more sustainable world, then AFCO wants to help. Because making a better world is our mission, too.
ENVIRONMENTAL STEWARDSHIP
We only have one world, so let’s treat it with care. We are dedicated to reducing our environmental impact and supporting customers by developing and implementing sustainable practices.
SOCIAL ACCOUNTABILITY
No investment pays better returns than investing in people. We are committed to safety in the workplace. Our training and technical services will empower your team members to develop skills to improve operational safety.
GOOD GOVERNANCE
Because of our commitment to the highest government standards and FDA regulations, we provide sophisticated data and reporting so you can optimize your business practices and risk management.
PARTNER
Provide solutions to help our customers achieve their sustainability goals:
Productivity Solutions
Energy Conservation Solutions
Water Management
Training Capability
PLANET
Reduce environmental impact
through sustainable practices:
Sustainable Industrialization
Operational Excellence
Climate Leadership
Water Stewardship
Eliminate Waste
PEOPLE
Promote health and well-being
of others and caring for our people:
Provide Safety
Teach Best Practices
Develop Skills for the Future
PRINCIPLES
Improve business practices
through responsible processes:
Transparent Reporting
Government Regulations
Compliance and Corporate Responsibility
Consistency and Standards
Case Studies
Examples of increased operational efficiency by providing custom solutions in the food and beverage industry
-
Increased production volume can have unintended side effects. Occasionally a manufacturer can be forced to use a 3rd party co-manufacturer to meet demand. In order to avoid this potentially costly outsourcing, attempts were made to optimize sanitation times and shorten the window, to allow more time for production, and keep manufacturing in-house. The implementation of a spray bar to apply cleaning chemicals to a conveyor belt was utilized to shorten the sanitation window.
-
Increased production volume can have unintended side effects. Occasionally a manufacturer can be forced to use a 3rd party co-manufacturer to meet demand. In order to avoid this potentially costly outsourcing, attempts were made to optimize sanitation times and shorten the window, to allow more time for production, and keep manufacturing in-house. The implementation of a spray bar to apply cleaning chemicals to a conveyor belt was utilized to shorten the sanitation window.
-
Cleaning of small and medium sized parts in a bakery can be a laborious process, requiring two employees to manually (foaming, scrubbing, scouring) clean all parts. This can lead to an unpredictable cleaning cycle, sometimes stretching into two shifts. The implementation of a COP tank allows the facility to partially automate the cleaning process, saving money on labour and ensuring an adequate cleaning in a consistent amount of time.
-
A common way to confirm that sanitation is complete is the examine the pH of rinsate from equipment following cleaning procedures such as a caustic boil-out in a fryer, to ensure no residual chemical remains in the system. If relying solely on water to neutralize residuals following a boil out, the neutralization process can take hours and hundreds of gallons of water before the rinsate is at a neutral pH value, and a facility can proceed with production. The introduction of an acid product to the first rinse cycle was able to drastically reduce the time required to achieve a neutral pH, and return to production.
-
The production of potato chips can release large amounts of grease during the cooking/frying process. This airborne grease can deposit on virtually any surface in a chip manufacturing facility and can provide unique challenges for a sanitation team. Traditional cleaning of this environmental grease can require a full shift using a scissor lift and scrubbing tools to remove. Often two stages of cleaning are required as traditional products will not adhere to ceilings and vertical surfaces long enough to allow the chemical to begin to break down greasy deposits. The implementation of AFCO 2601 Oven Gen Cleaner allows a manufacture to reduce cleaning time by 5 hours and avoid the use of lifts to reach high areas.
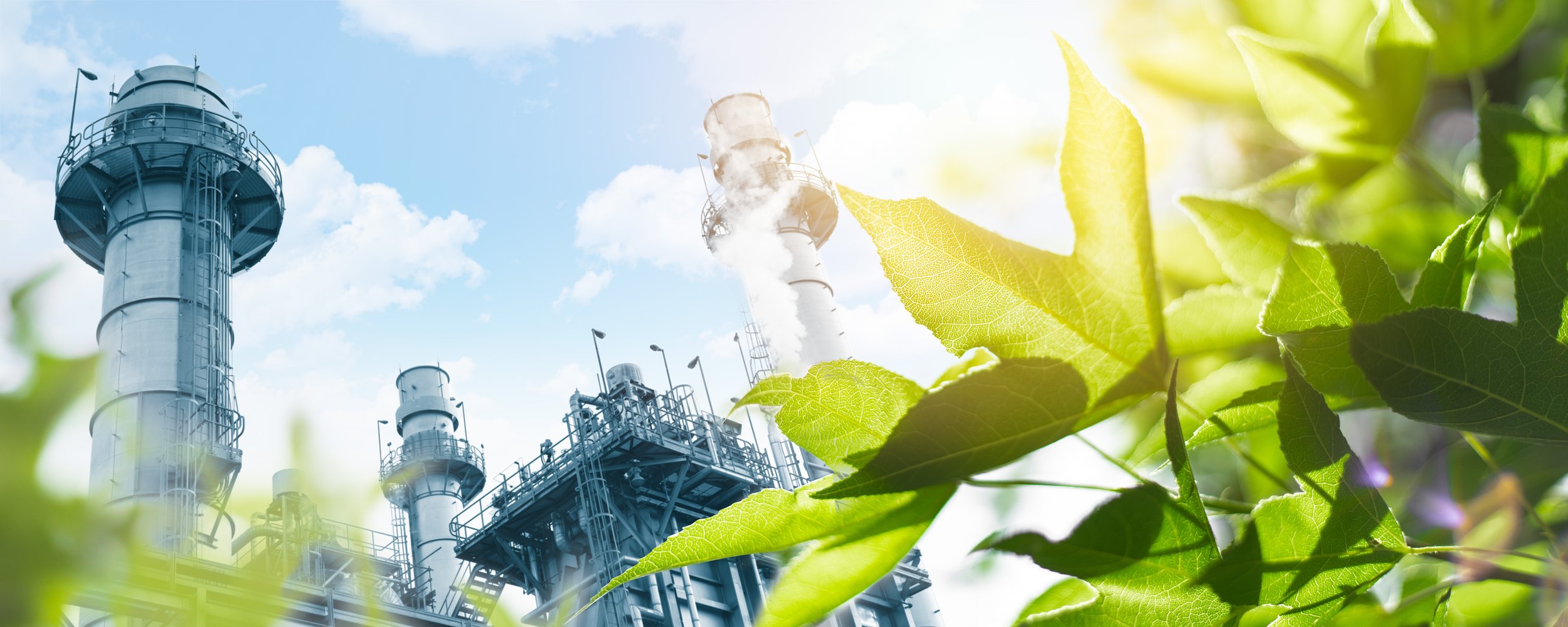